Comprehending Porosity in Welding: Checking Out Causes, Impacts, and Avoidance Methods
As professionals in the welding industry are well aware, understanding the reasons, effects, and avoidance techniques associated to porosity is vital for achieving durable and dependable welds. By delving right into the root triggers of porosity, analyzing its detrimental effects on weld high quality, and exploring efficient prevention techniques, welders can boost their knowledge and abilities to produce high-quality welds continually.
Usual Root Causes Of Porosity
Contamination, in the form of dust, oil, or corrosion on the welding surface area, produces gas pockets when warmed, leading to porosity in the weld. Incorrect securing occurs when the securing gas, typically made use of in procedures like MIG and TIG welding, is not able to totally protect the liquified weld pool from responding with the bordering air, resulting in gas entrapment and succeeding porosity. Additionally, insufficient gas insurance coverage, commonly due to wrong flow rates or nozzle positioning, can leave components of the weld unsafe, allowing porosity to develop.
Effects on Weld Top Quality
The presence of porosity in a weld can substantially endanger the general top quality and honesty of the welded joint. Porosity within a weld produces gaps or dental caries that compromise the framework, making it extra prone to fracturing, deterioration, and mechanical failing. These voids act as anxiety concentrators, reducing the load-bearing capacity of the weld and boosting the likelihood of premature failure under applied anxiety. Additionally, porosity can additionally function as potential websites for hydrogen entrapment, further exacerbating the destruction of the weld's mechanical homes.
Furthermore, porosity can hinder the performance of non-destructive screening (NDT) methods, making it challenging to discover other defects or interruptions within the weld. This can cause considerable safety problems, particularly in essential applications where the structural honesty of the bonded components is extremely important.

Prevention Techniques Overview
Given the harmful effect of porosity on weld high quality, efficient prevention methods are crucial to keeping the architectural honesty of bonded joints. In addition, picking the appropriate welding parameters, such as voltage, current, and take a trip rate, can assist lessen the threat of porosity development. By integrating these prevention techniques into welding methods, the incident of porosity can be substantially minimized, leading to stronger and much more dependable bonded joints.
Value of Correct Protecting
Appropriate shielding in welding plays a vital role in avoiding atmospheric contamination and ensuring the honesty of welded joints. Shielding gases, such as argon, helium, or a mixture of both, are commonly made use of to secure the weld pool from reacting with components in the air like oxygen and nitrogen. When these reactive components enter contact with the warm weld swimming pool, they can cause porosity, bring about weak welds with lowered mechanical homes.
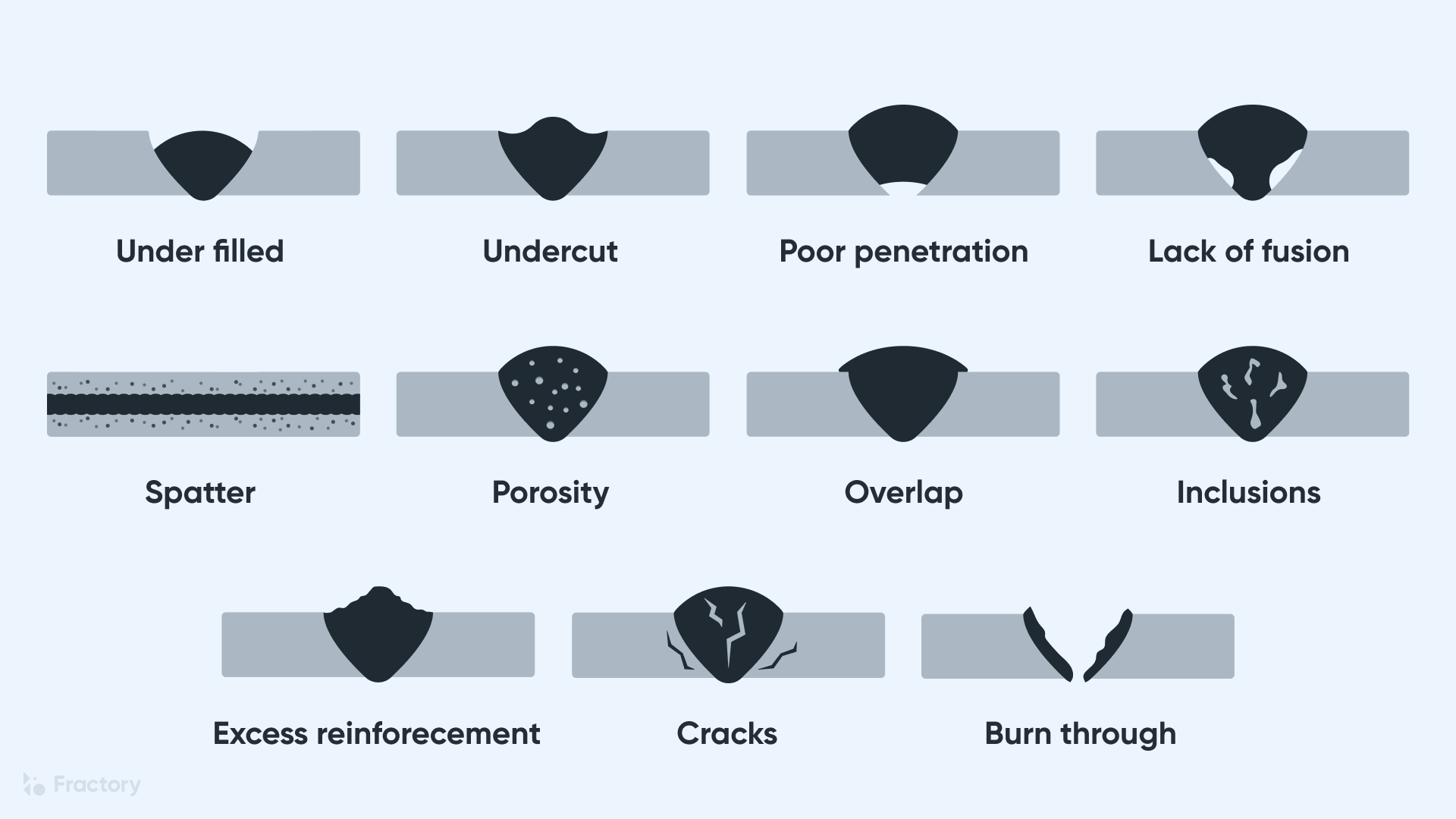
Insufficient shielding can lead to various flaws like porosity, spatter, and oxidation, endangering the structural honesty of the welded joint. Consequently, adhering to appropriate securing techniques is important to generate top quality welds with marginal problems and make certain the longevity and integrity of the welded elements (What is Porosity).
Surveillance and Control Methods
Exactly how can welders efficiently monitor and regulate the welding procedure to make certain optimum outcomes and protect against problems like porosity? One key approach is through making use of sophisticated surveillance modern technologies. These can include real-time monitoring systems that supply feedback on criteria such as voltage, current, travel speed, and gas circulation prices. By continuously keeping track of these variables, welders can determine variances from the perfect problems and make immediate adjustments to What is Porosity avoid porosity formation.

Additionally, applying correct training programs for welders is necessary for keeping an eye on and managing the welding procedure efficiently. What is Porosity. Enlightening welders on the importance of keeping constant specifications, such as appropriate gas protecting and travel see this here rate, can assist prevent porosity concerns. Routine analyses and accreditations can also make certain that welders are skillful in tracking and controlling welding procedures
In addition, using automated welding systems can enhance tracking and control capabilities. These systems can exactly regulate welding parameters, lowering the likelihood of human error and making sure consistent weld high quality. By combining innovative surveillance modern technologies, training programs, and automated systems, welders can successfully monitor and manage the welding procedure additional hints to reduce porosity defects and accomplish top quality welds.
Final Thought
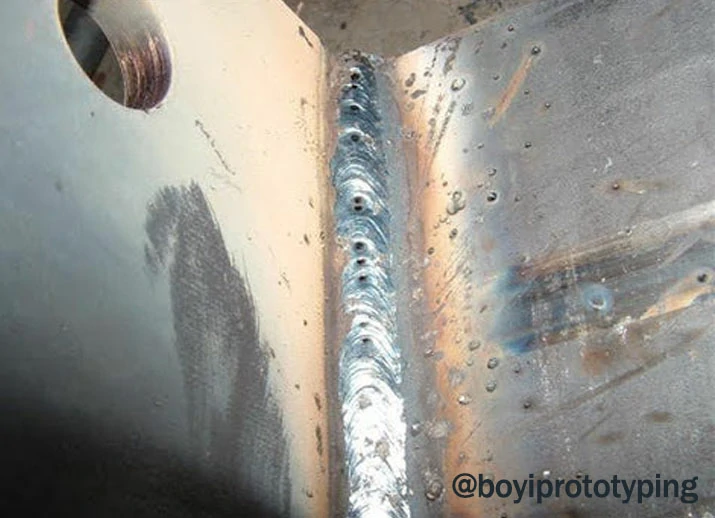
Comments on “How to Recognize What is Porosity in Welding and Improve Your Technique”